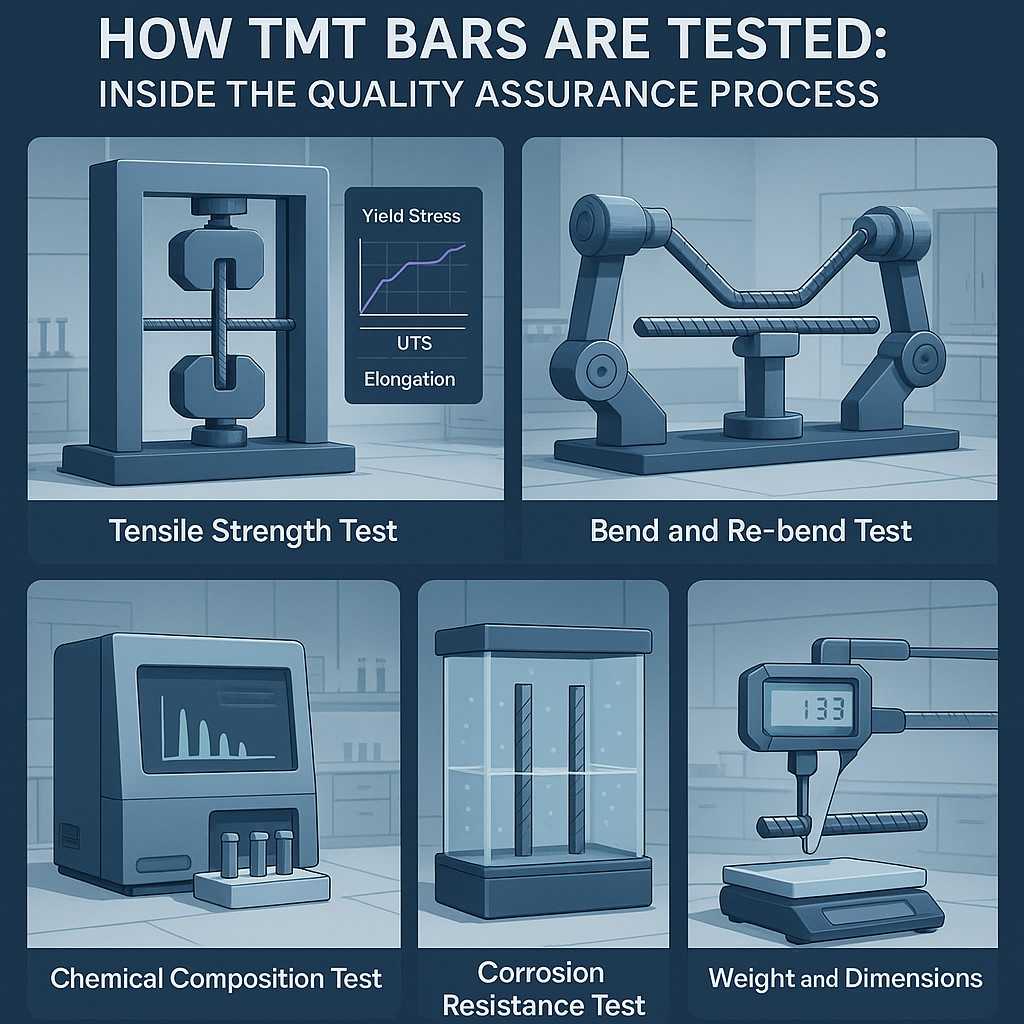
In construction, strength is not a guess – it’s a guarantee. And when it comes to TMT bars, that guarantee is forged in steel labs long before a bar ever reaches a building site.
From a 3-storey home in Raipur to a 15-acre logistics park in Pune, contractors and developers alike have something in common: the demand for reliability. But how do they know the TMT bars they use won’t fail under load or weather? The answer lies in the rigorous quality testing that bars like APL Apollo SG TMT undergo before dispatch.
In this blog, we pull back the curtain on how TMT bars are tested – and why these processes matter more than ever in today’s high-stakes construction landscape.
A Real-World Starting Point: Why Testing Isn’t Optional
Earlier this year, a mid-size contractor working on a luxury villa project near Hyderabad received a batch of TMT bars from an unfamiliar supplier. Visually, everything looked fine. But within two weeks of binding the reinforcement for the first floor slab, multiple bars began showing signs of flaking and rust – indicating poor corrosion resistance.
What followed was a delay, a safety audit, and eventually, a complete replacement using Fe 500D grade TMT bars from APL Apollo SG Infra.
The cost of rework? Over ₹3.5 lakh. The lesson? TMT bar testing is not just a manufacturer’s duty – it’s a buyer’s shield.
How Are TMT Bars Actually Tested?
Whether the end application is residential, commercial, or industrial, trusted manufacturers like APL Apollo SG TMT follow a layered approach to testing:
- Tensile Strength Test (Yield Stress, UTS, Elongation)
Using a Universal Testing Machine (UTM), a sample TMT bar is pulled apart until it breaks. This reveals:
- Yield strength (the point at which deformation begins)
- Ultimate tensile strength (max load before breakage)
- Percentage elongation (indicating ductility)
Real Insight:
APL Apollo SG TMT Bars consistently meet and exceed Fe 500/Fe 550/Fe 500D grade standards with high elongation—especially valuable in seismic zones.
- Bend & Re-bend Test
The bar is bent 180° and then straightened partially to test for surface cracks or brittleness. This checks the bar’s flexibility and grain uniformity.
On-site Relevance:
In high-rise projects like those seen in Gurgaon or Navi Mumbai, workers often bend TMT bars to fit specific formworks. Failure in re-bend performance can compromise joints.
- Chemical Composition Test
Done using a spectrometer or lab-based analysis, this test verifies levels of carbon, sulfur, phosphorus, and other alloying elements.
Why it Matters:
Low carbon levels = better weldability.
Low sulfur/phosphorus = enhanced corrosion resistance.
APL Apollo SG TMT Bars follow IS:1786 standards to the letter, ensuring clean steel that’s ideal for RCC work and durable even in saline coastal areas like Chennai or Kochi.
- Corrosion Resistance Test (Salt Spray/Water Immersion)
Bars are subjected to moist or saline environments to simulate exposure and check for rusting. This is particularly relevant for infrastructure projects (flyovers, bridges) or basements in flood-prone zones.
Case in Point:
APL Apollo SG Infra bars, designed specifically for infrastructure use, undergo advanced corrosion resistance treatments—making them ideal for municipal and highway projects.
- Weight and Dimensional Accuracy Test
This test ensures that an 8mm or 16mm bar actually matches the declared diameter and weight/meter ratio. Underweight bars are a common trick used by unbranded suppliers to lower prices.
Also Tested with:
MS Binding Wire, which is used to tie TMT bars in place during RCC work. Uneven or low-quality wire can result in loosened reinforcements or poor cage alignment.
Explore how our MS Binding Wire ensures durable tie-ups in high-load structures.
How Buyers Can Check if a TMT Bar Has Been Tested
Even if you’re not a structural engineer, there are simple ways to verify the quality of the steel you’re buying:
- Ask for the manufacturer’s Mill Test Certificate (MTC)
- Look for the BIS mark and batch number on the bar
- Request lab reports if ordering in bulk
- Prefer bars from brands with in-house labs and third-party testing (like APL Apollo SG)
And if you’re dealing with intricate rebars for footings or columns, make sure the MS Binding Wire is also from a certified source—it plays a subtle but critical role in long-term stability.
In Summary: Testing Is the Foundation of Trust
When someone stands inside a home, works in an office tower, or crosses a metro bridge, they trust that the structure above them won’t fail. That trust is built not just with concrete and steel -but with quality checks, certifications, and rigorous testing standards.
TMT bars like those from APL Apollo SG aren’t chosen just because they’re strong – but because that strength is proven, recorded, and consistent.
Next time you’re sourcing materials – whether it’s for a bungalow in Bhopal or a warehouse in Surat – don’t just ask for the TMT price today- Ask for the test report. Ask for the proof.
Because safety doesn’t come from specs alone – it comes from steel that’s been tested, and passed with integrity.
Coming Up Next in the Series:
“The Role of MS Binding Wire in RCC Structures – Small But Mighty”
Pingback: Why Ductility Matters: Fe 500D & Fe 550D TMT Bars for Seismic Safety